Automation with Linde: Level Up Your Performance
Hit the High Score!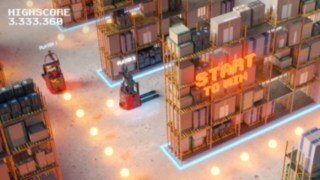
Welcome to the intralogistics gaming zone! Here we are taking your storage and transport processes to the next level, making them smarter, faster, and more innovative. Our driverless transport systems and autonomous logistics trucks are real game changers! They handle monotonous, repetitive tasks, take a load off your employees, and boost your productivity.
With our MATIC range, you can feel the power of automation. These high-tech players easily integrate into your warehouse environment and get your processes up to speed, making them safe, efficient, and fit for the future. Ready to get started? Then make an appointment for a consultation with our team of experts and get your intralogistics game off to a great start. Let’s play!
START – Select Your Quest
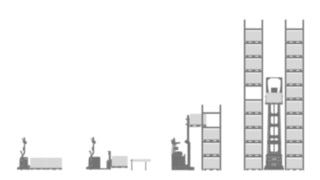
Game on! Find your AGV challenge
From the challenges of high rack storage to the need for speed on the warehouse floor: Automation makes light work of your warehouse and transport processes. Each stage of the process is its own quest, which you can tackle with our automated guided vehicles (AGVs). It’s all about skills, speed, and strategy. Are you ready? Then let’s begin your first mission!
Quest 1: Horizontal Transport from A to B
Your mission is to master efficiency and accuracy in warehouse logistics by transporting goods and materials between different areas of a warehouse or production facility. This includes standardized processes such as moving goods or empties, maneuvering pallets and heavy loads (including in mixed traffic), and transferring loads between the floor and conveyor technology. Your playing field is a maze of paths and stations that extends into all areas between goods in, storage, production, and goods out. In this game, every second counts and every move has to be spot on.
The players: L-MATIC AC, C-MATIC and C-MATIC HP (AMR)
Quest 2: Low Lift, Pick & Drop, Conveyor Belt
This round is all about optimizing the floor logistics in a warehouse or production facility. For this, you need to master three key processes of intralogistics: low-lift transport, pick & drop, and transferring loads from floor to conveyor belt (and vice versa). You will move pallets efficiently at ground level and interact with the material handling technology in the warehouse. To achieve this, you have use of an automated pallet stacker, which records the exact position of the load and features comprehensive safety equipment.
The players: L-MATIC HD
Quest 3: From the Floor to Medium Heights
In this part of your intralogistics challenge, you need to pick up goods and materials from the floor, deliver them precisely to their destination, and set them down again on the floor or at medium height, for example, at transfer points to the high rack warehouse. This is crucial to ensuring the many components are in the right place at the right time. This task entails traveling between various areas, from goods in, to the warehouse, production halls, and goods out.
The players: L-MATIC AC
Quest 4: Working at Medium and High Heights
This mission is about transporting goods and materials to medium to high storage areas. Your goal: To use shelves and storage areas as efficiently as possible, therefore optimizing the entire warehouse logistics. This involves being on the move in all areas of the warehouse, and participating in various processes. For example, you might temporarily place incoming goods on racks in the goods in area, deliver material for removal to goods out, or retrieve pallets from the rack in order for them to be used for manual picking on the floor. To achieve this, you have an automated reach truck at your disposal. Thanks to its compact design, it is highly maneuverable and agile. In addition, it can interact with a variety of storage systems (standard racking, flow racks, conveyor systems, etc.), and it enables you to safely place loads even at great heights.
The players: R-MATIC
Quest 5: Storage and Retrieval in the High Rack Warehouse
This mission takes place in the dizzying heights of a high rack warehouse. The challenge is to store and remove all goods quickly and safely up in the high racks, and to make them available for picking. To complete these tasks, you have an autonomous turret truck available, which can interact independently with the upstream and downstream infrastructure in the warehouse process (such as conveyors or transfer stations). Equipped with modern navigation systems and safety devices, it allows for precise maneuvers around the tight spaces in the narrow-aisle racking.
The players: K-MATIC
BONUS POINTS: The Advantages of Linde Solutions
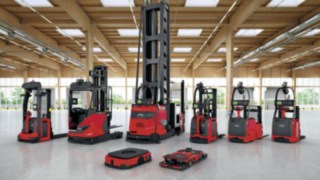
Your Reliable Gaming Buddies
With Linde, you can master any automation challenge. We have successfully launched hundreds of automatic solutions worldwide. We have the largest network of service technicians in the industry, with 8,500 of them ensuring that your automated trucks and solutions are always ready to go and available for your missions at all times. With Linde’s automated trucks, you also have access to our trusted Linde Service.
DEMO – Customer Success Stories
Do you still need inspiration for your own warehouse games? Then sit back and relax and see how others have solved their quests with the help of automation. Industry, 3PL, automotive, packaging and many other sectors: Discover which companies are already profiting from the game-changing benefits of Linde solutions.
-
Electrical Engineering—Fully Automated Shipping Logistics
-
3PL—Automation of Storage and Retrieval
-
Chemistry—Optimizing Safety and Efficiency
-
Packaging—Automated Pallet Transport to the Warehouse
-
Paper—Automation Despite Constantly Changing Environmental Change
-
Food—More Space, More Storage, More Efficient Logistics
-
Automotive—Automation in Long, Narrow Aisles
-
3PL—Automation of Goods Flows
-
Electrical Engineering—More Productivity in the Logistics Center
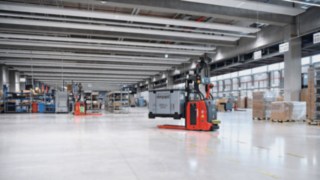
Electrical Engineering—Fully Automated Shipping Logistics
- The challenge: At the Mulfingen site, ebm-papst is looking for ways to optimize its shipping logistics.
- Linde solution: Linde experts analyze the material flow in order to find efficiency potentials. To implement the changes, Linde uses one of its partner companies for logistics solutions. Three automated Linde L-MATIC pallet stackers are introduced and connected to ebm-papst’s internal SAP Extended Warehouse Management System. The automated trucks exceed the required transport capacity and boast an impressive availability rate at almost 100 percent.
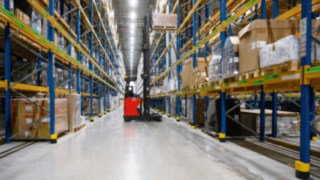
3PL—Automation of Storage and Retrieval
- The challenge: The contract logistics company FIEGE has to cope with extreme seasonal fluctuations with up to 10,000 packages and 4,500 Euro pallets per day at peak times. The company is looking for technical solutions that are easy to implement without changing existing racking systems.
- Linde solution: Linde recommends the R-MATIC for this task. Just three weeks after the start of the automation project, the driverless reach truck is already in operation. The R-MATIC uses a 3D camera to identify the pallet type and allows for precise placement even for high shelf levels.
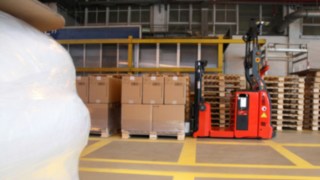
Chemistry—Optimizing Safety and Efficiency
- The challenge: BASF is a global chemical company that mainly produces additives for plastics in Italy. The plant in Bologna is part of the global logistics and production network and works according to high safety standards. As such, Linde’s automation solution has to adhere to the strictest safety protocols.
- Linde solution: A Linde driverless transport system optimizes safety in the packaging area. The strength of this solution lies in its maximum configurability. The truck communicates directly with the packaging system and therefore knows exactly when to remove a finished pallet or to supply the process with an empty pallet.
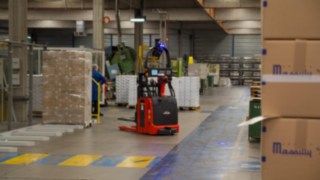
Packaging—Automated Pallet Transport to the Warehouse
- The challenge: The French packaging specialist Massilly already fully automates its cans production, including printing, stamping, forming, and welding the sheet metal parts. Now for the final stage of the process, they want to automate transport to the warehouse.
- Linde solution: Automated Linde L-MATIC pallet stackers transport pallets from the packing station to the high rack warehouse. Their routes are adaptable and do not require additional infrastructure such as laser reflectors or rails. Linde provides regular training in the use of automated equipment in order to actively involve staff in the upgrade.
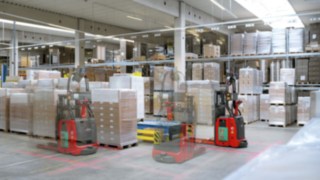
Paper—Automation Despite Constantly Changing Environmental Change
- The challenge: Paper specialist Franz Veit wants to automate its in-house goods transport, because traditional transport methods between production and the stretching machines are inefficient and time-consuming.
- Linde solution: Two autonomous Linde L-MATIC pallet stackers are put into action, which independently navigate the space thanks to natural feature navigation, and find their way around in a constantly changing environment without any problems. The performance of the automation solution exceeds expectations, and the workforce welcomes the support provided by the new technology.
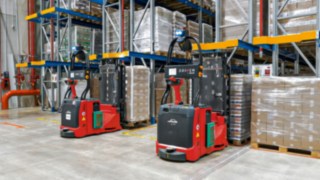
Food—More Space, More Storage, More Efficient Logistics
- The challenge: Madi Ventura, a company that produces nuts and dried fruit, has to massively expand its production area due to continued growth. The company needs a scalable logistics solution that can interact with the existing system and manual processes.
- Linde solution: Linde installs a new high rack warehouse with additional pallet spaces, and supplies automated Linde K-MATIC very narrow aisle trucks and autonomous Linde L-MATIC AC pallet stackers. A massive 98 percent of the tasks are handled flawlessly by Linde automation solutions, and the storage capacity can be doubled.
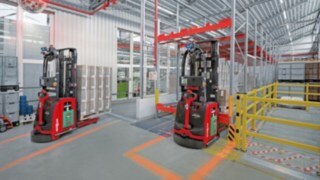
Automotive—Automation in Long, Narrow Aisles
- The challenge: The automotive supplier Oechsler AG wants to use automation to optimize its logistics processes at the headquarters in Ansbach, Germany. They must overcome severely cramped conditions in the warehouse aisles and very long driving routes, including an intermediate ramp.
- Linde solution: Linde analyzes the material flows and simulates the number of pallets to be transported. A little later, three Linde L-MATIC HD automated pallet stackers start work. Among other things, they supply the flow rack and automatically identify vacant storage spaces. They store pallets at heights of up to four meters, and are in use 24/7. Their comprehensive safety technology protects pedestrians in the mixed operation warehouse. No structural changes are necessary for the implementation.
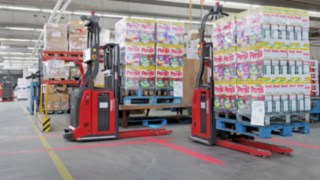
3PL—Automation of Goods Flows
- The challenge: Since the site opened in 2014, Henkel’s logistics partner TST GmbH has been carrying out manual transport processes, which are becoming increasingly problematic. The company wants to make its processes safer and more efficient through smart automation.
- Linde solution: Five automated Linde L-MATIC pallet stackers are launched to transport goods from finishing stations to the stretching machine without having to interfere with the infrastructure. The project is implemented in just eight months and has so many benefits that automation is to be extended to other locations.
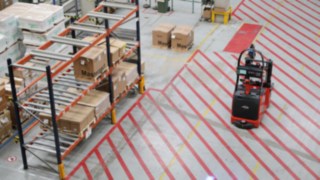
Electrical Engineering—More Productivity in the Logistics Center
- The challenge: Due to changing market conditions, energy and automation specialist Schneider Electric decides to automate some areas of its intralogistics to increase efficiency at its Spanish site in Sant Boi de Llobregat.
- Linde solution: After comprehensive analysis and appropriate preparation of the site, Linde supplies two automated Linde L-MATIC AC pallet stackers. The implementation of the automated trucks helps to improve the control of the material and shorten the routes that employees have to travel.
TEAM SPIRIT—We Are on Your Side
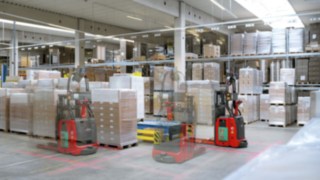
Our automation solutions allow you to create more efficient processes and take a load off your employees. This frees up your capacity to boost your company’s productivity. We’re here to support you every step of the way. That’s our idea of team spirit!