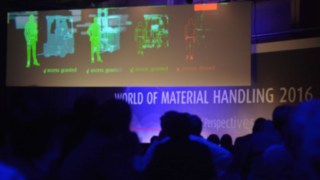
The information superhighway runs right through warehouses
9 May 2016
At WoMH, Linde Material Handling demonstrates the opportunities created by digital networking
As is the case in so many industries, logistics processes, and thus the flow of materials, are increasingly being directed digitally. As a result, even industrial trucks are becoming a part of digital industry. Whether with universally electronically controlled trucks, the innovative sensor technology found in Linde Safety Pilot, the connect: fleet management solution or other digital solutions, Linde Material Handling has laid the foundations to be able to support its customers in the digitalisation of their business processes. At ‘World of Material Handling’ (WoMH), Linde will exhibit – among other things – a new localisation technology which allows the location of trucks or transport containers in warehouses and production halls to be recorded in real time to within a centimetre. This information has a wide variety of applications, significantly improving the efficiency and safety of operational processes. The gap between the real and digital worlds has already been bridged.
Visitors to WoMH 2016 can experience the precision and versatility of this technology at first-hand: guides and experts will be carrying transmitters with them, and their location on the premises will be displayed in an app on the tablet which every guest will be given at the beginning of their visit – extremely helpful if you lose sight of your tour group. What’s more, the performance of the drivers on the WoMH kart track can be monitored second-by-second – the electric karts, made by Italian manufacturer CRG, are not only fitted with Linde drive systems but also with localisation transmitters. “Using this real time tracking system as a basis, we will expand the functionality of our connect: product family, as well as developing new applications which will go above and beyond fleet management,” explains Massimiliano Sammartano, Linde’s Vice President of Sales & Service Marketing & Operations.
Virtual zones and analytical tools for path planning
The cost-effective localisation solution was developed by Linde together with tracking specialists Quantitec. In this system, ‘nodes’ are installed in warehouses or production rooms. These nodes allow the tracking system to determine the position of the transmitter on the truck in the room. This makes it possible, for example, to divide up the warehouse into virtual zones and then within those zones apply rules and permissions for drivers and trucks – regarding speed and lifting height, for instance. “Plus, the continually-recorded position of the forklifts can also be saved in a sort of ‘heat map’, showing the paths the trucks take in a certain time frame,” explains Colin Flint, head of Product Marketing for Linde Connected Solutions. “In the future, this will allow us to help our customers to optimise path planning for their fleets and reduce the risk of accidents in busy areas.”
All connect: fleet management functions to be demonstrated on site
Indoor localisation won’t be the only technology demonstrated on the WoMH kart track, however: “Our work together with our partners CRG has not only involved developing the electrical drive system for their karts based on the drive technology in Linde’s electric forklifts – they were also very interested in our fleet management solutions,” says Wolfgang Klüpfel, project manager for Linde eMotion. As manufacturers of karts for rental and racing, CRG’s customers are kart track operators whose requirements overlap in many ways which those of a fleet manager. This is why CRG offers Linde’s connect: solution to its customers, alongside the karts themselves. Access control, adjusting driving parameters for different drivers, collision detection using shock sensors, maintenance scheduling, recording and usage analysis – all functions and information which aid the operators of both karts and industrial trucks in making their fleet as safe and efficient as possible.
Improved safety and truck availability through networking
WoMH promises another innovation for the connect: fleet management solution, too: the connect: app ‘pre-op check’. This allows the forklift driver to check over their truck at the beginning of a shift for important things such as tyre pressure or possible damage, using a smartphone. The forklift is unlocked only after being checked with the app. Meanwhile, the “connect: desk” software combines the information with other data and analyses it. This not only improves safety, but also improves the productivity and availability of the trucks. Trucks can be equipped with connect: units during manufacture, or they can be easily retrofitted at any time. There are numerous options for data transmission: mobile service, Bluetooth or a wireless network – whichever is most suitable for the customer’s infrastructure. Individual driver permissions and forklift settings can be configured, and the employee unlocks the truck using PIN or RFID.
Safety-relevant applications such as this are based upon an innovative sensor technology, which is also the basis for intelligent driver assistance systems such as the Linde Safety Pilot (LSP). LSP actively intervenes in forklift steering in critical driving and lifting situations, while also providing additional helpful functions such as load measurement. Already available for electric forklift trucks, the system will also be available for IC trucks in the near future. “We at Linde are definitely market leaders with regard to the productivity and safety of our trucks. In the future, however, the key to increasing efficiency in logistics and intralogistics will no longer simply involve the trucks themselves,” says Christophe Lautray, Linde’s Chief Sales Officer, “but rather the integration of the whole fleet into IT processes. At the WoMH, we will be demonstrating how that can work.”
Faster responses: Mobile Service Manager app
Linde is also keen to offer more transparency in service activities in the area of customer service going forward, and will present an application which is currently undergoing testing. With the Mobile Service Manager app, operators using Linde trucks will in the future be able to address their inquiries to Linde’s service organisation directly using the QR code of the truck and a photo of the malfunction. They will then be kept up to date on the current status of their inquiry via their smartphone. The existing ‘MyLife’ extranet system will then allow fleet operators to view information about the current workload, age distribution and maintenance status of the fleet, including a transparent overview of costs. “MyLife is aimed primarily at buyers and logistics managers at larger companies,” explains Dieter Antensteiner, Head of Fleet Management. “The data makes planning fleet compositions easier, and therefore also facilitates investment decisions. The focus is on cost efficiency.”
The future of intralogistics: WoMH demonstrates a wealth of ideas and solutions
Under the title ‘Linked Perspectives’, the World of Material Handling event will provide answers to the biggest questions which intralogistics will face in the future: not just networking, but also automation, individualisation and energy systems. "Internal logistics will increasingly be networked, digitalised and automated," states Sammartano. Spanning over a space measuring 12,000 square metres, the event will feature exhibition areas, 3D-media shows, expert forums, product demonstrations and experience zones. The exhibits can be demonstrated as part of guided group tours or visitors can discover them on their own. “Following on from the comprehensive exhibition two years ago, we are concentrating this year on the four most significant areas of expertise which will be of vital importance for our customers in the very near future,” explains Manfred Höhn, Head of Marketing Communication and Branding.