Automation, next level: Linde Material Handling creates facts
Milestone on the way to autonomous outdoor forklifts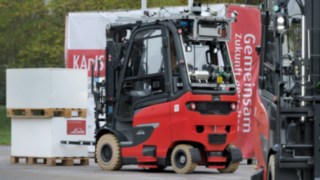
Maximum safety in the flow of goods, optimal deployment of employees, a shortage of skilled workers, sustainable safeguarding of competitiveness: it is no coincidence that the topic of automation is at the top of the agenda for many logistics managers. And it goes without saying that their wish list does not end with the automated pallet trucks and the like that are already established in many places.
For Linde Material Handling as a driver of innovation, this is a clear mandate to intensively push the development of autonomous counterbalanced trucks: trucks that are completely driverless in indoor and outdoor areas, pick up and transport goods, load and unload trucks and much more. A highly complex field with various sub-disciplines for which specific solutions have been developed. Linde presented these after almost four years of research work with the Aschaffenburg University of Applied Sciences (UAS) as part of the KAnIS (Cooperative Autonomous Intralogistics Systems) project.
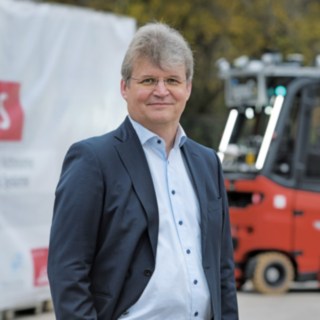
The university has the scientific expertise - we have the technical know-how. This enabled us to develop functional prototypes together very quickly.
Stefan Prokosch, initiator of the KAnIS project, Linde Material Handling
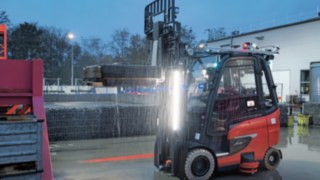
Automation and outdoor areas: a sophisticated combination
What makes the development of autonomous forklift trucks so challenging is primarily to do with the classic application scenarios of such devices; after all, these often extend to outdoor areas such as depots or block storage facilities. In contrast to clearly defined indoor sections, the environmental conditions there are far more dynamic: potholes must be safely avoided, slopes or inclines must be mastered and a wide variety of road users must be taken into account. Uneven floors and road profiles also influence driving behavior. And then there is the whole range of weather influences such as fog, rain or snow, which pose enormous challenges for the installed sensor technology. In other words: a multitude of variables - and for the KAnIS project partners a multitude of tasks, which were addressed in several sub-projects.
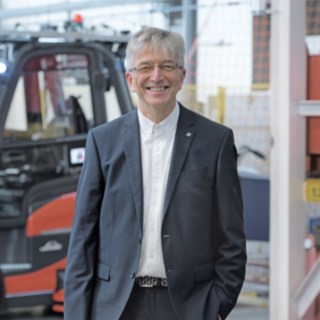
The KAnIS project was a very complex, interdisciplinary research project for Aschaffenburg UAS. Ten professors were involved, along with numerous research assistants and students.
Prof. Dr. Hans-Georg Stark, Project Manager KAnIS, Faculty of Engineering, Aschaffenburg University of Applied Sciences (UAS)
Attentive, responsive, proactive ...
Ideally, human forklift truck drivers should have these "virtues" when they go to work - and autonomous vehicles should be designed like that in terms of software and hardware! The KAnIS researchers therefore focused their work on these aspects: Environmental perception and interaction with other road users. Sophisticated 3D laser scanners and HD cameras play an important role. While the latter are particularly well suited to recording colour information and recognizing and classifying objects with the help of AI algorithms, laser scanners are the technology of choice for determining the distance to the classified objects. The result: the forklift truck knows what is happening in its environment and can act appropriately.
... and also prepared for the worst-case scenario
But what if, for example, a person suddenly moves towards the forklift from an area that is not visible? In such critical situations, the researchers are focusing on cooperation - along the lines of "I can see what you can't". If another forklift truck has detected the person, this information is sent to a server via an ultra-fast private 5G network (specially set up as part of the project), which in turn forwards it to all other forklift trucks. And if there is no other truck nearby? Here too, Linde Material Handling and Aschaffenburg UAS have made provisions: in the form of stationary 3D laser scanners that are placed at neuralgic points and also transmit their data to the central server.
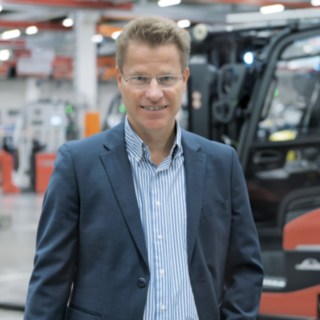
Fast wireless networks are a prerequisite for autonomous forklift trucks to be able to act cooperatively outdoors and react to unforeseen traffic situations in real time.
Prof. Dr. Klaus Zindler, Vice President Research and Transfer, Aschaffenburg University of Applied Sciences (UAS)
A lot of research for the work assignment
Of course, much more is needed to turn an autonomous forklift truck into an all-round reliable, productive logistics assistant. For example, counterbalance trucks - the "Swiss army knife" of industrial trucks - are known to have to cope with a variety of load carriers. The project participants have created the prerequisites for recognizing and recording these by installing a movable camera mounted between the forks. It measures the respective load carrier so that the forks can be positioned accordingly via the sideshift. Keyword position: while the forklifts use laser scanners to localize themselves in indoor areas, a particularly precise differential GPS is used for outdoor applications. The research team's specifications also included topics such as predictive maintenance, automatic load management and options for automatically cleaning sensors close to the ground using compressed air.
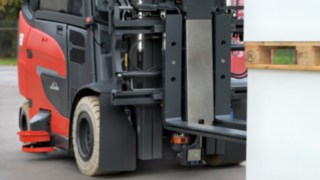
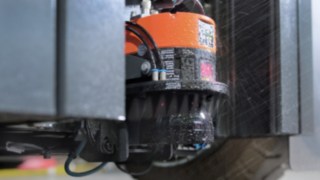
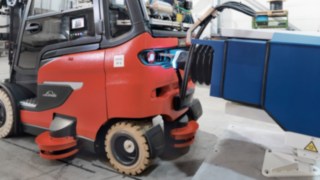
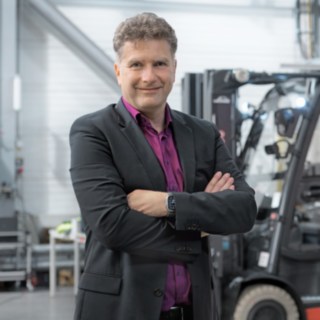
The practical implementation of the research findings was an important aspect for Linde Material Handling and Aschaffenburg UAS.
Mark Hanke, a Head of Department in Pre-Development, Linde Material Handling
Four autonomous forklifts make a start
It was clear to Linde and Aschaffenburg UAS right from the start of the project: KAnIS should not only deliver theoretical results, but operational prototypes. Specifically, the technology carriers built are four vehicles based on the Linde E20, Linde E25 and Linde E30 electric counterbalance trucks. The plan is to develop these further over the course of 2024 and improve their practical suitability so that they can be used under real conditions at the Aschaffenburg plant in the future.
Both indoors and outdoors, the high-tech devices will be used to transport pallet cages, palletized batteries or vehicle frames, for example, while negotiating gradients of up to 8 percent and interacting with other people and AGV systems. And: they will provide Linde with further valuable insights to ensure that the application-oriented research ultimately results in a marketable product for customers.
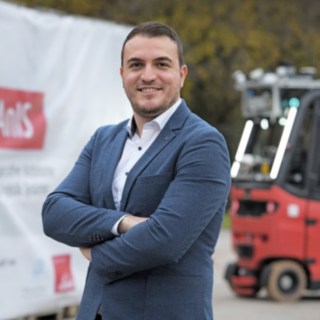
We are not only the research partner, but also the first customer of the project.
Mal Rexhepi, Product Manager Automation and Intralogistics Solutions, Linde Material Handling