Veltins Brewery relies on lithium-ion battery-powered forklift trucks
A thirst for innovation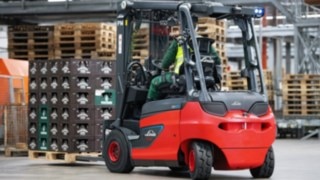
Anyone brewing and bottling millions of hectoliters of Pilsener beer, shandy, malt beer, apple beer and other mixed beer beverages needs powerful intralogistics systems to get the drinks onto the street. C. & A. Veltins, a brewery with a rich tradition, has put its faith in forklifts from Linde Material Handling for this demanding role. Gradually, the electric forklift trucks have been converted tolithium-ion technology,which avoids the need for time-consuming battery changes and improves availability.
Everyone knows that in logistics, you sometimes have to move mountains. At the C. & A. Veltins brewery this happens on a daily basis, with the aid of some 65 industrial trucks: mountains of filled bottles and empties need to be loaded and unloaded, taken into and out of storage, and moved back and forth between the various parts of the business. Even so, with the best will in the world, one mountain that cannot be moved is the hill on which the brewery complex sits, with its commanding views over the picturesque town of Grevenstein in the Sauerland hills of western Germany. Thanks to this hill, not only are the plant’s operations spread over various different levels, but they also involve tight spaces that are constantly taxing the logistics department with a need for new solutions. “For example, the sloping site severely restricts the options for classic block storage facilities,” explains Logistics Manager Benedikt Flügge. He and his colleagues are thus continually on the search for new approaches that can help them organize the flow of goods not only more efficiently but in particular in a more compact manner. The flow of goods at Veltins is quite unique, not least because of the matter of the “empties”.
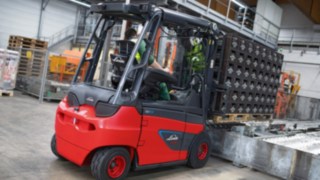
When a truck loaded with empties from a drinks wholesaler arrives in the loading bay at the foot of the company site, the pallets of empty bottles are first unloaded by forklift and then, using an automated materials handling system, transported to the production hall one level above. In a parallel operation, the handling system also shifts out a pre-assigned batch of filled bottles that is loaded back onto the vehicle by the same forklift truck. The entire loading and unloading process for a truck takes just 25 minutes on average. The empties are then pre-sorted at the first level of the production hall, from where a conveyor belt takes them upwards again to the sorting center. Here, the crates are recorded on camera and the empties then sorted entirely automatically. This complex technology handles 7000 crates an hour. “Processing the empties is quite a colorful process—firstly because of the growing variety of bottles and crates,” says Flügge of this demanding activity, “and secondly because all sorts of containers end up on the pallets of empties.” Once sorted, all the intact refillable bottles are carried automatically back downhill to the filling plant, where they are cleaned, filled, labeled and picked for dispatch.
Room for good ideas
300,000,000 liters—a three followed by eight zeros, or more simply, three million hectoliters— that’s how much Veltins Pilsener and other varieties of beer flowed through the taps of the filling plant in 2018 alone. And this is where the family-owned brewery launched its “venture into conversion”, two years ago now, from lead-acid batteries to the modern lithium-ion equivalents. “At the time we were running three Linde E14 forklift trucks for transport jobs in the filling plant, all with conventional lead-acid batteries,” reports Logistics Manager Flügge. “Sure, they were reliable in service, but changing the batteries every day and keeping them in good condition involved a certain amount of work. Lithium-ion technology promised marked improvements in this regard.” The first step, with Linde network partners Richter Fördertechnik, was to analyze and test whether the local electricity supply was up to the task. Another area for discussion was how the chargers should be distributed around the site. “We started with two of the 1.4-metric-ton forklift trucks, which we subjected to intensive testing for a considerable period. In the beginning there was a degree of skepticism among our people,” recalls the Veltins Logistics Manager. But after a few short weeks, the new processes had become second nature. “Staff have made interim recharging of the batteries a regular part of their work process.”
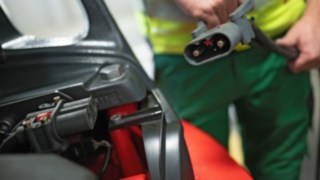
A solution with a longer-term perspective
Logistics managers were encouraged by their positive experiences in the bottling plant so it was not long before the decision was taken to invest further in the new battery technology. In the returned bottles handling area and in pre-picking, a total of three electric forklift trucks with lead-acid batteries had previously been deployed. “Today,” relates Flügge, “we manage the same tasks with two Linde Roadsters with lithium-ion batteries.” In no small measure, this is down to the higher availability of the lithium-ion equipment. In deciding where best to position the two 63-amp charging units, Theo König, Branch Manager at Richter Fördertechnik, again supported company with advice. “One of them is sited on the way to the breakout room, so staff can recharge their forklifts while they’re grabbing a coffee.” Thanks to regular interim recharging such as this, the trucks are always available throughout all three shifts, and it is only at weekends that they are plugged into the chargers for longer periods. Fewer servicing activities and better protection for workers also make life easier—
the lithium-ion batteries require no daily or weekly maintenance such as topping up with water.
Flügge continues: “And what’s more, we don’t need to worry about harmful battery gases any more.” On the question of why the Roadster was chosen, the Logistics Manager continues: “The special design without A-pillars means that our drivers have a broader field of vision, which improves safety, given the tight working spaces and the long prongs on the truck.” This is confirmed by forklift operator David Conze: “With the Roadster, I get a much more direct view of what’s going on around my truck, and with the reinforced glass roof I’ve got a great view upwards as well.”
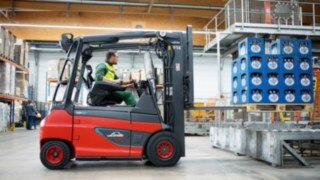
Moving around
Top of the list: On the floor of the sorting center, too, along a steep and winding road from the loading area, there is plenty for a forklift truck to do. Vast quantities of third-party goods are loaded, in a demanding four-shift system: “When it comes down to it, the trucks are on the go 23 hours out of 24,” stresses Flügge. That’s no problem for the 3.5-metric-ton electric forklift trucks in use there, with their lithium-ion batteries. And the innovative battery technology has proved its worth in setting up the displays, too: with the aid of a Linde E14, Veltins puts together quarter- and half-pallets for its customers. The brewery supplies some 70,000 of these displays a year to the retail trade, and the figures are rising because in cities in particular, customers are keen to pick up a handy six-pack that will fit into any shopping basket.
The suspense continues
The brewery is currently testing out whether even the heaviest transport jobs—loading and unloading the long-distance delivery trucks with full bottles and empties—could be handled by electric forklift trucks. Until now, this work has been handled by six Linde H80 diesel forklift trucks, each with a 6-pallet capacity—loading up to 200 delivery trucks a day. “For us it would be a logical step to test the new battery technology for the 8-metric-ton forklifts as well,” says Logistics Manager Benedikt Flügge. And so far, it’s looking very good for the E80 Li-ion.
Acceleration, lifting power, speed—the performance and availability of the trucks are just right. An 8-hour shift loading and unloading trucks is no problem. And the drivers are very content too, as they sit somewhat higher up and therefore get a better view into the truck.
Looking to the future, Logistics Manager Flügge states, “If possible, we want to aim to switch to lithium-ion forklifts across the board and get away from the complicated battery-switching process.” For the new store that the brewery is currently planning on the site, a lithium-ion forklift is again under consideration to take on the loading of export containers. “At the end of the day, though, it’s the way the forklift is used that determines what form of energy makes the cut.”
Taking a longer view, managers at Grevenstein envisage that even fuel cell equipment might be added to the mix. Flügge adds: “With that sort of technology, there are still a few hurdles to overcome, but we do see ‘cold combustion’ as the energy source of the future.”
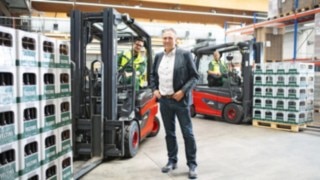
The brewery, C. & A. Veltins GmbH & Co. KG, was founded in 1824. The company is based in Grevenstein, which is part of the town of Meschede, North Rhine Westphalia. It currently employs a staff of over 650 and has an annual turnover of some 350 million euros. Its fleet of Linde trucks includes 65 trucks in total, the vast majority on full-service leasing contracts managed by Linde network partner Richter Fördertechnik. All the trucks are fitted with front and rear cameras,Linde BlueSpot™,various LED warning lights, and additional safety features depending on where and how they are used as well as electronic access control via the fleet management systemLinde connect.