How two automated assistants ensure efficient goods transport
Keeping Goods Moving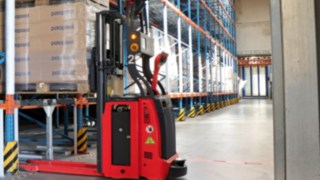
If demand, and therefore the production volume, increases, this is actually a cause for celebration. But how can you manage the increased flow of goods without burdening employees with more and more repetitive transport assignments? At the plastics processor Poloplast, the answer is automation, made by Linde Material Handling.
“And now to the traffic: the roads are all clear today and everything is moving freely without any obstructions. So, have a great day everyone!” This is the kind of news that will cheer you up on the way to work or when you leave for the evening. If your actual working day is also free of traffic jams, so much the better. When it comes to the latter, the employees of Poloplast GmbH & Co. KG in Leonding, Upper Austria, are in luck—that is to say they have two automated LindeL-MATIC pallet stackers.
Looking Back: Towers of Goods in Production
At Poloplast, one of the leaders in the European piping industry, over the years constantly increasing production volumes resulted in a substantial congestion problem for a certain product range. This is because, in addition to large pipes for sewer systems etc., the company also produces smaller items for the domestic drainage sector. These are packed into boxes and then loaded, partly by hand and partly automatically, onto Euro-pallets. The task of getting finished pallets from production to the warehouse always fell to the colleagues on the early shift, who used a tugger train to transport goods from Monday to Friday. “We work seven days a week here in a four-shift system. When the people started work in the mornings, things would have accumulated overnight—to say nothing of the situation on Monday mornings. Then it was as if the entire weekend’s output was piled up in production”, explains Poloplast’s Head of Logistics Ralph Wagenhuber.
It was obvious that they needed to think about automation.
The people responsible at Poloplast already had relatively specific ideas when they started to look at suppliers. Wagenhuber says, “Of course, we wanted to achieve the highest possible level of reliability, but at the same time we also wanted a solution that would fit into our existing infrastructure without major changes—i.e. without mirrors, guide rails and so on—so that we could adjust the routes easily if necessary.”
In addition to this, thesafety aspect was quite high on our list of specifications, because ultimately there are always a lot of trucks and pedestrians moving between the production area and the warehouse. “This ‘wish list’ led us relatively quickly to Linde Material Handling, which was already fairly well represented in our forklift truck and industrial truck fleet anyway”, explains Head of Logistics Wagenhuber.
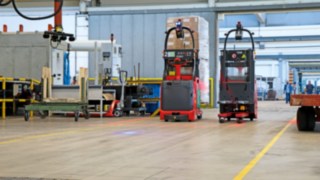
The autonomous trucks have the “map in their head” …
Working with the goods handling experts from Aschaffenburg, two Linde L-MATIC autonomous pallet stackers were implemented at Poloplast during the course of the project. The trucks, which have been affectionately christened Tom and Jerry, use geo-navigation to move completely independently (and of course quietly) between the drive-through warehouse and the total of nine pick-up stations. Eight of them are manually operated, meaning that employees pack pallets with boxes and call the Linde devices at the touch of a button once they are ready.
There is also an automatic winding machine, which is approached independently by the pallet stackers and “relieved” of the packed and wrapped pallets.
… and are perfectly integrated into the processes
On their way into the warehouse Tom and Jerry pass roller shutters, which communicate with the trucks via comboxes and therefore open and close automatically. Once they have arrived in the drive-through warehouse with gravity roller conveyors, the Linde L-MATICs also detect which of the seven conveyors is currently free. Wagenhuber says, “We have installed a light barrier for each shelf for this purpose. If a compartment is full, the Linde device is informed of this via the combox and moves on to the next free space.”
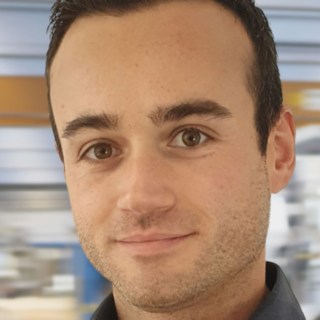
Frankly, we could hardly imagine how things would work here without the two Linde L-MATICs now.
Ralph Wagenhuber, Head of Logistics at Poloplast
State-of-the-art Systems Ensure Safety
Independently loaded and unloaded, and independent charging. This is all part of the service from Tom and Jerry. “If they do not currently have a job, when the devices reach around 40 per cent battery energy they go the charging station and replenish their power supplies for around 15 minutes. With these short interim charging breaks we ensure that the two of them can be on the move almost 24/7”, Wagenhuber says with satisfaction. In Leonding they are also happy with the comprehensive safety concept from Linde Material Handling: Tom and Jerry not only draw attention to themselves with theLinde BlueSpot™; the trucks also use LED lights to project easily visible red stripes onto the hall floor to the side and in the direction of travel. And, of course, the devices stop automatically as soon as a person comes too close to the front.
Output: Increased—Flow of Goods: Guaranteed
If you watch Tom and Jerry at work and see how they calmly get their tasks done (in stark contrast to their famous animated namesakes), you could almost forget that the job the trucks do is far from an easy one. The highly efficient pair load, transport and unload almost 60,000 pallets year after year. “Frankly, we could hardly imagine how things would work here without the two of them now. The people on the early shift no longer have to struggle with the long transport routes, we have gained space for new machinery and we have been able to significantly increase our output thanks to the continuous flow of goods”, says Wagenhuber, weighing up the benefits. “Nobody has to worry about congestion here.”
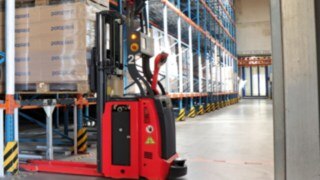
Poloplast GmbH & Co. KG
Poloplast GmbH & Co. KG is a plastics processor based in Leonding, near Linz in Upper Austria, and is one of the sector leaders in the European piping industry. The company, which operates internationally, predominantly develops, produces and sells reinforced, multi-layer piping systems made of plastic for the domestic drainage sector, but also for sewer construction. Together with its subsidiaries, Poloplast currently has around 370 employees. When it comes to intralogistics, the plastics specialist mainly relies on trucks from Linde Material Handling, and in addition to the two L-MATIC autonomous trucks, electric and diesel counterbalanced forklift trucks are also used in Leonding.