A DISCUSSION ABOUT AUTOMATION IN PRODUCTION LOGISTICS
Autonomous or manual?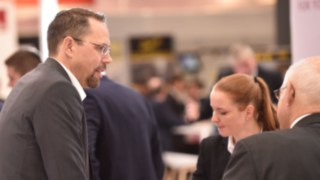
Automation promises greater efficiency in production logistics. However, in some cases a manual or partially autonomous scenario can be more cost-effective than fully autonomous operation. Digitalization expert Frank Heptner explains what makes the difference. He is Senior Director of Sales & Realisation Automation and Intralogistics at Linde Material Handling.
Mr. Heptner, you recently stressed in a talk that a fully automated production warehouse is not “automatically” the most cost-effective. Why not?
As is often the case in complex areas, the answer is that it depends. Numerous factors play a role, and these factors determine the right solution. With an increasing degree of automation, the digital networking of different areas is much more pronounced, leading to increased complexity. Blanket statements would therefore fall short of the mark.
To what extent does that apply to production logistics in particular?
In production supply, we are under considerable pressure to operate efficiently. The manufacturer’s customers expect short delivery times, a wide variety of products and a high level of flexibility at the same time. In order to keep up with this, major logistical modifications are necessary in some companies.
What modifications are needed?
Broadly speaking, the three pillars are “flexibility, versatility and scalability.” Companies become more flexible when they optimize their structures and material flows. Increased versatility means that existing production environments can be expanded more easily and can be adapted to the new demands on a modular basis. For improved scalability, an efficient logistics strategy and, ideally, autonomous logistics processes are needed. Digital networking is essential for all three pillars. It’s just a matter of achieving the right level of automation, depending on the available equipment (for example, industrial trucks and material handling technology), the production environment, the available processes and the load carriers to be transported.
Which standard do you use for this?
In the most advanced cases, operations are already fully autonomous today. This means that driving, loading and unloading are completely automated. At the other end of the scale, there are fully manual operations. In between, partially autonomous solutions have been established, whereby either driving or loading and unloading are automated. In general, there is a trend toward fully autonomous systems. However, not all autonomous systems are cost-effective. That’s why a precise process analysis is required for every project.
There is a trend toward fully autonomous systems. However, not all autonomous systems are cost-effective. That’s why a precise process analysis is required for every project.
How are process analyses like this carried out?
First of all, we record the infrastructure with all information processes and determine the project requirements together with the customer. Based on this, we assess the technical possibilities and prioritize solutions. The core of the analysis is a comprehensive automation matrix. We put together this matrix so that we can compare all solutions available on the market. In the process, the solutions were assessed in terms of their suitability for various processes and load carriers. For each project, we identify all necessary transport processes and load carriers. We then take the potential solutions from the matrix for each of these processes. After that, we calculate the cost-effectiveness. We assess all transport solutions in consideration of the volume, calculate the return on investment and the marginal costs, and also take qualitative factors into account. We establish the qualitative factors together with the customer and rate each of them. This final evaluation takes account of the structures the company has developed and its areas of focus, such as occupational safety, sustainability or ergonomics. Customer A, for example, attaches particular importance to flexibility, while maintaining the highest safety requirements. By contrast, for customer B, the handling capacity with a minimal error rate is of paramount importance. These factors ultimately determine if they should invest in a solution and, if so, what type of solution this should be (partially or fully automated.) This consideration must be made for each project individually and together with the customer, in order to take the various requirements into account.
In which cases would you still recommend a manual solution?
That depends on the productivity of the transport methods used, for example. If a manual single unit or double-deck transport system is often used in a warehouse, for example, the degree of transport efficiency may be low, but at the same time the level of flexibility in the event of route changes is deemed high. On the other hand, a manual bundle transport system may be very efficient, but driving flexibility is lower. Depending on how well suited the methods used are to the production environment and the load carriers, it may be the case that we prioritize the manual solution.
Optimizing the manual processes can already lead to efficiency increases. In these cases, we recommend process optimization in the first instance, and only later recommend an automation.
Could there not also be a cost-effective fully automated solution for these cases?
We are examining this question thoroughly with the help of the solution matrix. Autonomous vehicles are often more efficient, but it’s not just about that. A tugger train with autonomous P-MATIC tow tractor is virtually unbeatable when it comes to transport efficiency, but is it also best suited to the production warehouse? Or does the operation preferably need a solution that offers maximum flexibility in the event of route changes, due to its warehouse structure and material flows? If so, something like a turtle solution would be the right choice in the field of autonomous vehicles, although this does have a lower degree of transport efficiency than certain manual solutions. What's more, with partially autonomous systems, autonomous vehicles also need to move around in the working environment of people and serve them without the risk of accidents. In short, partially or fully automated logistics usually actually present a more efficient scenario. In that case, the cost of the investment is crucial. Furthermore, optimizing the manual processes can already lead to such efficiency increases that we suggest a process optimization in the first instance and only recommend an automation at a later date. By doing so, we help the customer make a sound assessment for the long term with the right course of action.
What is the level of acceptance among customers for your automated solutions?
We have already implemented many partially automatic processes for large load carriers and order pickers, usually with autonomous transport and manual loading and unloading. As automated vehicles, it is mainly the Linde MATIC solutions with intelligent natural feature navigation that have proven successful. They already cover 80% of all handling activities today. Fully automated large load carrier solutions are, to date, manageable in production, as cost-effectiveness is still a hurdle at many transfer points. For applications with few transfer points, fully automated projects have already been realized. With small load carriers, the first systems for partially automated processes are in use, usually with automatic driving. For fully automated processes, we are carrying out pilot projects to establish economically viable solutions. We are confident that new approaches will emerge that will soon be able to take the supply processes in production to the next level.