Heidelberger Druckmaschinen AG
A breath of fresh air in logistics at Heidelberg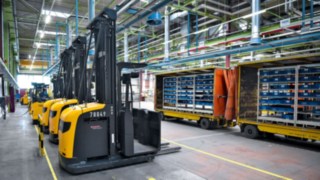
In times of increasingly individualized customer requirements, intralogistics must also gradually adapt to the changed production conditions. How this can be achieved by a global industrial company is shown by the example of Heidelberger Druckmaschinen AG (Heidelberg) in Wiesloch/Walldorf. Together with Linde Material Handling and its contract partner Suffel Fördertechnik as general contractor, the company set up a completely new logistics concept, which optimizes the supply of materials to the assembly lines of offset printing machines.
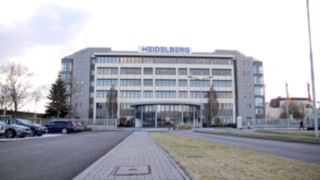
The brightly colored cornflakes packaging on the breakfast table, the trendy glossy magazine during the coffee break or the elegant business cards at a business lunch: although our modern world is becoming increasingly digital, we remain in constant contact with printed matter and printed goods everywhere we go. And, as different and diverse as these may be – the likelihood that they were produced on a Speedmaster by Heidelberg is fairly high. After all, the world-famous company, with 11,500 employees, is a leading player in the industry. The printing specialist's head office is located in Wiesloch/Walldorf, Baden-Württemberg – in the heart of the economically strong Rhine-Neckar metropolitan region, where the busy north-south transport routes of the A5 and A6 intersect. This is where Heidelberg operates the largest and most cutting-edge printing machine factory in the world; machines including the market leading sheet-fed offset printing machines in various format classes are manufactured in an area covering a square kilometer.
New challenges –
New Concepts
Heidelberg has been observing a steady change towards greater individuality in the area of customer requirements for a number of years: "Previously, we predominantly built similar printing machines at each site," remembers the Head of Plant Logistics Matthias Ehmler. "Now, we frequently manufacture customized systems and because of this, there has been a sharp rise in the number of different versions," he explains.
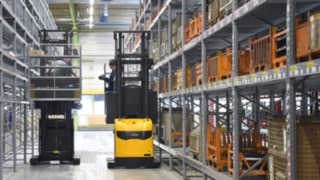
Linde reach trucks and order pickers in the Heidelberger Druckmaschinen warehouse
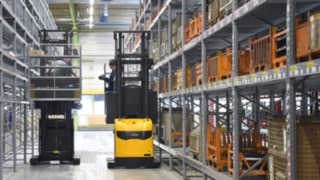
Linde reach trucks and order pickers in the Heidelberger Druckmaschinen warehouse
This customizing trend ultimately also affects the assembly lines: "Workers at the assembly stations were increasingly moving between unmanageable 'material mountains'. The greater the variety, the more parts containers were required. This had an increasingly negative impact on employee productivity," Ehmler explains. "As a result, two years ago, we launched a project to reorganize the assembly department. We wanted to use the production areas more efficiently and bring the material to the worker, not the other way around."
The restructuring of the assembly department towards a modular construction included a reorganization of the intralogistics in the 600-meter-long hall. In future, materials with low daily requirements will no longer be provided in containers on site, rather they will be ordered and picked on kit carts and introduced to the assembly lines by load trains. A central order picking and consolidation area with high racks was set up at the front end of the assembly hall for this purpose. Upstream buffer zones were specified as interfaces for the internal transport systems and as transfer stations for the kit carts.
"Our aim was to ensure a safe, efficient and flexible material supply with the best possible use of the available space," explains the Head of Heidelberger Factory Logistics. An ambitious project, whose implementation during ongoing operation required the perfect meshing of all the different cogs.
Competent partner required
The individuals responsible entered the tender phase with an extensive requirements specification. "We were looking for a partner to implement the rack construction and equipment with industrial trucks, including fleet management, as a general contractor." Ehmler outlines the task facing the logistics companies involved: "At the same time, the time and cost schedule agreed with us naturally also had to be complied with, so that we could focus entirely on managing the basic data and providing training for employees". The decision to award the contract to the manufacturer and solution provider Linde Material Handling together with its contract partner Suffel Fördertechnik was based on a number of reasons: "First of all, the Linde equipment was impressive, with its unique technical features – such as the bar trolley trailers for the load train, and the high level order picker. And, secondly, we were impressed with the consultancy and naturally also the terms of the contract," reports Ehmler.
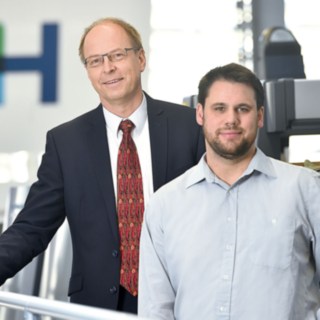
"Rack construction and industrial trucks from a single source proved to be a success for us in every respect."
Matthias Ehmler, Head of Factory Logistics
To enable order-based provision of the parts to the assembly lines, it was necessary to first find a suitable solution for the order picking warehouse – and therefore for the centerpiece of the new logistics concept: "We already had a number of specific ideas and guidelines in the requirements specification. After the contract was awarded, these were gradually developed together with Linde and Suffel. The order picking warehouse had to allow the storage of large and small parts as well as entire assemblies and different container geometries, while also satisfying the high occupational health and safety standards," says Project Manager Stefan Heger, summarizing the major challenges.
Well-organized supermarket
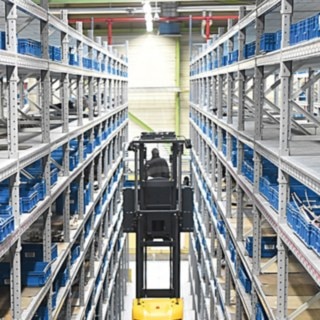
The new high rack warehouse with 13 rack rows and 4,500 part numbers acts as a supermarket and consists of a wide-aisle area with an aisle width of 4.05 meters and a narrow-aisle area with three lanes. In the wide aisle, three Linde R14 reach trucks are responsible for storing the material, while, in the narrow aisle, the seven Linde V modular order pickers take over picking tasks as well as the replenishment of supplies. The warehouse is stocked from three different sources. Large load carriers reach the picking area via a bridge connection from the directly adjacent central supply warehouse. Small load carriers are pre-picked in a separate automatic small parts store and delivered via the internal transport system. Completions take place as required in the pre-assembly area, which is connected to the picking area.
Ergonomics and safety play an important role
Only Linde V modular high level order pickers are used for picking in the high racks. Using the truck, employees pick the required material from heights of up to 6.50 meters and stock the approximately 1.80-meter-high and 1.60-meter-wide
wire mesh kit trolleys, which can bear a maximum weight of 500 kilograms. Up to three picking orders are placed on a kit trolley. The high level order pickers have integrated tilting barriers to enable employees to reach easily into the storage bay. "This equipment option is a genuine unique selling point for Linde, which we were able to fully utilize in our new high racks", emphasizes Jens Kernbach, Head of Hall Logistics at Heidelberg. "Because, Heidelberg is also feeling the effects of demographic change and we are responsible for our employees."
To ensure that the picking process is "seamless" in the truest sense of the word, the equipment within the rack aisles is induction operated. This means that the operator can focus entirely on the picking process while traveling at an optimal distance to the rack. Another piece of equipment is the aisle safety assistant, which applies the brakes to the equipment bringing it to a controlled stop where necessary. "We can now rule out any damage to the rack or to
the equipment," says Project Manager Heger contentedly. The incoming stock is also secured with light barriers. They immediately trigger an alarm if unauthorized personnel enter the area that is only approved for trucks. In addition, Linde semi-automatic warehouse navigation is pre-installed in the equipment and offers potential for further optimization. This RFID-supported solution allows the high level order pickers to navigate in the rack aisle in an optimum characteristic curve to the instructed space without any action by the operator.
"The inductive lane guidance allows us to rule out damage to the rack and the order pickers."
Stefan Heger, Project Manager
Flexible and compact with load trains
A total of three Linde Load Trains transport the stocked kit trolleys from the transfer station to the workers on the production lines. They consist of a Linde P50 tow tractor as the tractor unit, and one or two bar trolleys with all-wheel steering and wide lift lips. Every trailer enables the simultaneous transport of two kit trolleys, which can be positioned and removed on either side thanks to the lack of a central axle. "This gives us flexibility when planning routes," says Project Manager Stefan Heger. Another advantage is how little space is required by the Linde load train, which holds its line when traveling along a lane 2.20 meters wide.
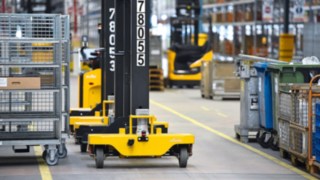
Positive outcome, but optimization continues
Even after the completion of the investment, factory logistics head Ehmler remains on the search for further optimization potential. He expects the "Use Analysis" module of the Linde fleet management solution to provide assistance. Says Ehmler: "We have already been using 'connect:' to control the truck access and to record shocks for many years and can look back on an extremely positive experience. We can now also use the software to optimize our processes and, for example, to further increase the utilization of the equipment."
It is now coming up to one year since the redesign of the intralogistics was implemented at Heidelberg based on the high rack warehouse, high level order picker and load train principle. And as one might imagine, the conclusion from Matthias Ehmler is favorable: "Not only did we implement the project within the planned time and cost framework, but also achieved our goal of streamlined logistics. Linde and Suffel have certainly made a positive impact on us."
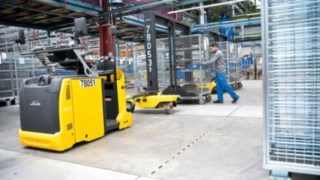