Eight-ton electric forklift in action at Mineralquellen Wüllner GmbH in Bielefeld, Germany
Electric power packs help to quench thirst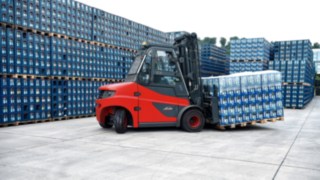
Heavy loads, demanding shift work, extensive terrain – and that with electric forklifts? What may sound quite unusual for some logistics specialists at first glance is everyday life at Mineralquellen Wüllner in Bielefeld. The family business, one of the top 20 producers of non-alcoholic beverages in Germany, has been using eight-ton appliances with electric drives from Linde Material Handling for several years now.
Extraordinary – this attribute best describes the main building of Mineralquellen Wüllner GmbH and Co. KG. Anyone approaching the extensive grounds from Bielefeld in an easterly direction will first be amazed by the futuristic building with its oval forms, shiny aluminium cladding and wide window fronts. Nevertheless, the almost spaceship-like construction blends perfectly into the gentle hilly landscape near the Teutoburg Forest. At least as impressive is the scenery on the area behind it: The beverage crates pile up here metres high, pallet on pallet – currently around 22,000 pieces – in block storage.
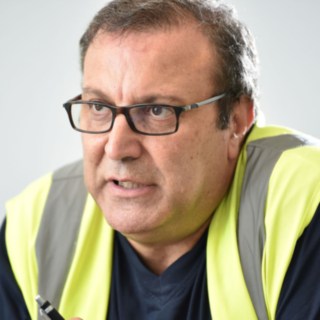
High load capacities, low energy and maintenance costs, an emission-free drive as well as very quiet driving noises – the Linde electric forklifts convince us right down the line.
Coneccto Cannizzo, logistics manager at the main location of the beverage manufacturer Mineralquellen Wüllner GmbH and Co. KG in Bielefeld, Germany
Efficient logistics
A fully loaded lorry is just leaving the company premises; the next trailers are already ready. Because the business with the crystal-clear element, which is mined here from a depth of around 300 metres, is going very well. "People drink significantly more mineral water today than they used to", explains Christoph Bisewski, marketing manager of the family business, which operates two other mineral springs in Saxony-Anhalt and Mecklenburg-Western Pomerania in addition to the Carolinen spring. "In the 1970s, the per capita consumption in Germany was 25 litres per year, today we stand at over 140 litres – and rising," he adds.
In order to keep pace with the constantly growing demand, efficient logistics are required. "On average, we handle our entire warehouse once a week," says Concetto Cannizzo, logistics manager at the beverage manufacturer's headquarters. Work is carried out in a two-shift system from 6 a.m. to 10 p.m., and employees are even on duty at night when demand is particularly high. A proud workload – both in terms of the length of service and the tonnages that Wüllner's forklift fleet has to cope with.
"The trucks have a load centre of 900 millimetres, are equipped with triple pallet forks and transport up to 240 beverage crates with a total weight of up to six tonnes per trip," reports Cannizzo. It is therefore all the more astonishing that only electric forklifts buzz around the yard of the traditional company founded in 1925.
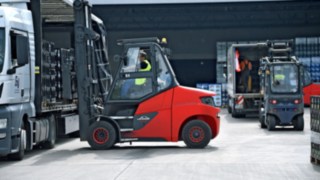
240 beverage crates per trip
The task of the electric forklift is to load and unload the lorries and to supply the filling plants on site. Once a week Mineralquellen Wüllner in Bielefeld handles the entire warehouse.
Sustainable approach
The company's self-image plays a major role in the decision to opt for the electric drive: "As a mineral fountain, we feel – naturally, so to speak – particularly committed to the environment," emphasises Marketing Manager Bisewsk. "Our main administration building, for example, is heated only with waste heat from the production area. With large-scale photovoltaic modules on the roof, we also generate the energy requirements of our forklift fleet ourselves. On the one hand, this is easy on the budget, on the other hand we are following our corporate philosophy in terms of sustainability".
At the same time, logistics boss Cannizzo emphasizes: "But our own electricity is only one argument. The fact that Wüllner only uses electric forklifts is also due to the fact that electric forklifts are emission-free and significantly quieter than internal combustion engine forklifts. This benefits our employees in the halls as well as our company neighbours, since traffic-related noise is regarded as the number one disturbance factor."
Convinced right from the start
The task of the five- and eight-ton electric forklifts is to load and unload the lorries and supply the filling systems on site. "We have been using Linde's high-performance trucks for three years now. Back then, Linde's sales partner Neotechnik provided us with a prototype of the Linde E80 electric forklift with a lifting capacity of eight tonnes," reports Cannizzo.
The electric powerhouse was quickly appreciated – and after a one-year test phase, further orders were placed. On average, the devices run for around seven hours with one battery charge – then the lead-acid batteries are replaced. A process that Wüllner very quickly carries out. "If no water is refilled, the actual change at the charging station takes less than three minutes," estimates Cannizzo and demonstrates the process himself as proof: "Open the side battery door, release the lock, lift out the battery with the forklift, turn it off, lift in the new battery – that's it. And he counters:
We would certainly have to calculate seven to eight minutes for refuelling a diesel lorry with a 65-litre tank.
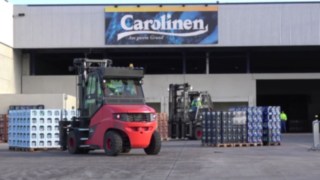
Precise and efficient
Keyword time advantage – the operating concept of the Linde forklifts is really well received by the employees. Cannizzo: "The double pedal control ensures fast reversing and shortens the time required for loading the lorry. Compared to competing vehicles, we are on average two minutes faster with one Linde electric forklift per lorry. That adds up to our handling performance."
A further plus point that, in the opinion of the beverage manufacturer, clearly speaks for Linde is the subject of comfort. "I used to drive forklifts myself and know how exhausting such a shift can be behind the wheel," reports Cannizzo. "At the same time, our employees are our success potential, so we would do well to provide them with a workplace that supports and motivates them. The employees particularly appreciate the heatable, air-suspended seats. Since the mast and axles are also uncoupled from the driver's cab, vibrations on board are noticeably reduced. And this has a positive effect on the drivers, especially as they spend a good part of their 3,500 working hours a year on the outside area, which is not always level.
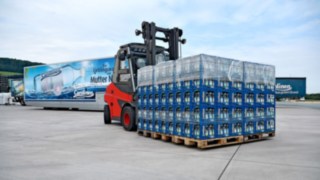
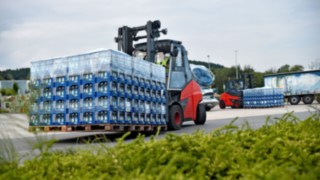
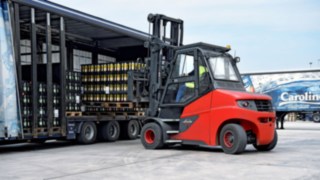

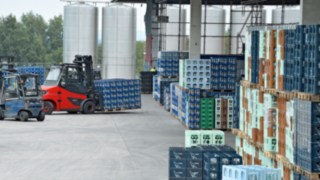
Playing it safe
In addition to the high load capacity, the robust protective roof of the electric forklifts, which forms a massive protection zone in conjunction with the cabin frame, ensures maximum safety when handling heavy loads. In consultation with André Kran, sales consultant at Linde sales partner Neotechnik, the forklifts were also fitted with Continental's CS 20 SE tyre, developed exclusively for Linde.
"CS" stands for "Closed Shoulder" and expresses that the outer tyre wall and tread form a closed shoulder and a closed area respectively. The advantages are smoother running, lower rolling resistance and, as a result, lower energy consumption. Added to this is the high traction provided by the double L-profiles. "Our drivers feel the continuous tread strip due to the significantly higher water displacement. And that means more safety in operation for us," explains Cannizzo.
Rare visit
A significant part of the high level of customer satisfaction is due not least to the one-stop shopping concept of Linde's partner Neotechnik for maintenance and service. "We have a permanent fitter who always comes when there is something to be done on one of the trucks. This has the advantage for us that he is very familiar with the forklifts and their attachments as well as on our premises". However, Cannizzo notes, his visits over the last three years have been limited to regular maintenance.
As far as reliability is concerned, the Linde machines are top! This is also reflected in the low costs for every single operating hour.
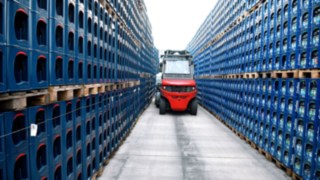
Outlook
The next major milestone for the family-owned company Mineralquellen Wüllner will be the completion of the new glass bottle production halls. The construction work is already in full swing. Once completed, they will also house the battery charging station with 28 charging stations for the forklift fleet. "With the improved infrastructure, we are equipped for the future," says Cannizzo. Regardless of battery technology, Wüllner's intralogistics are and will remain electric.